Space and Science: Capabilities
Rapid Response Precision Manufacture
We specialise in low volume precision engineering, offering a complete service for organisations in the scientific and space sectors. We’re not afraid to take on challenges that would deter most engineering companies and are used to working to tight production deadlines.
We provide a wide range of high-precision capabilities, from traditional milling and turning, to grinding and wire EDM. Engineering capability extends from large-bed 3-axis mills to high-speed 5-axis machines (700mm diameter) and large diameter lathes.
With an approved network of subcontractors to supply surface treatments to ISO, MIL, ASME and Aerospace standards we support one-off projects, prototype developments and initial production runs.
We pride ourselves on our quality. We are ISO 9001 certified, and offer a range of inspection capabilities, from 100% inspection using automated CMM or First Article reporting or basic dimension checks, to models depending on the requirement.
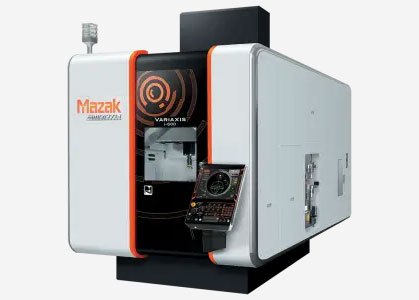
Milling
We run a Mazak workshop with the latest CNC milling machines suitable for almost every machining task. We have 3- and 4-axis mills capable of manufacturing parts up to 1000 mm x 600 mm x 600 mm – or 3000 mm x 800 mm x 720 mm on our large bed machine, clamping and feature dependent. Our 5-axis mills are capable of manufacturing parts up to 750 mm x 600 mm x 520 mm.
Turning
Our advanced CNC turning machines feature live tooling. Our lathes and mill-turn equipment can handle parts up to a diameter of 600 mm and lengths of 1550 mm. We have experience in a range of materials from Inconel through to engineering plastics, all grades of stainless steel as well as more traditional metals such as aluminium and titanium.
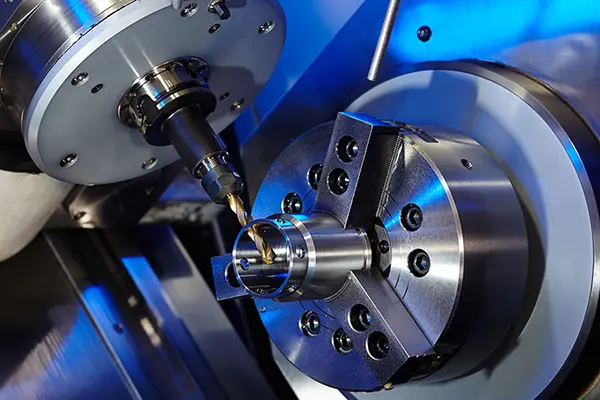
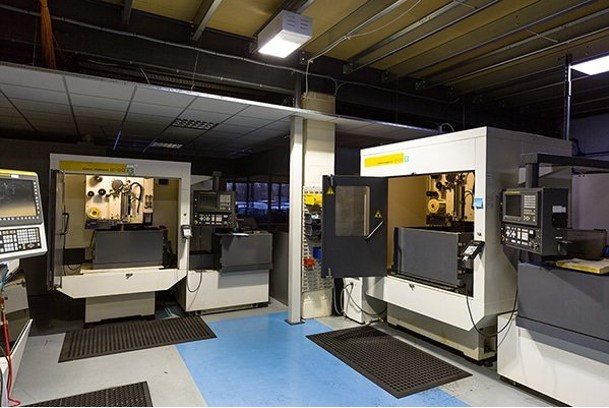
Wire EDM
Wire erosion is a great technique for cutting hard materials and complicated transitions. Our 4-axis wire EDMs can cut parts up to 600 mm x 400 mm x 310 mm tall.
Quality Assurance
We pride ourselves on our quality, offering 100% inspection on manufactured items. We are fully certified to ISO 9001, and provide certificates of conformance and full traceability for all our work.
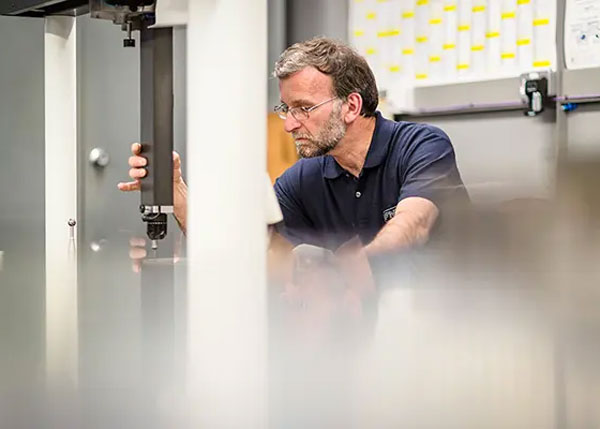
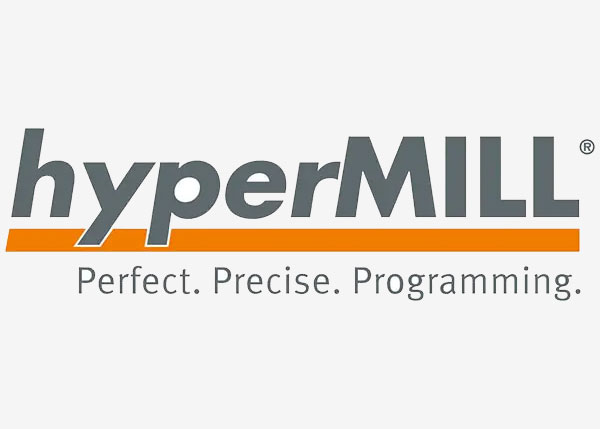
CAM
To ensure right first time manufacture we employ the latest CAM software in both our milling and turning functions. We are proud to have selected Hypermill as our preferred software solution.
Materials
We have extensive experience and expertise in working with standard materials such as regular carbon steels, stainless steels, hardenable steels, aluminium, brass, and plastics, as well as more exotic materials such as titanium and nickel alloys.
We are also experts in specialist surface treatments, including carbide, stellite and chrome, as well as proprietary processes such as Armoloy and Tufram.
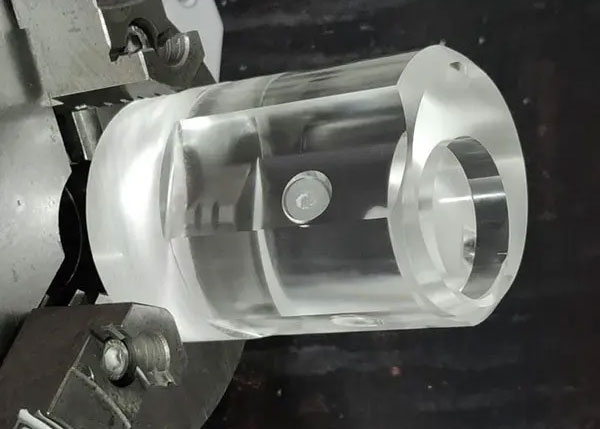
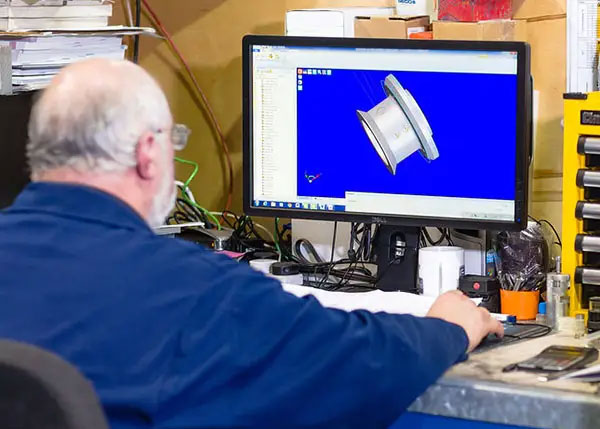
Project Management
Adding value to precision engineering
For our customers in the space and scientific sectors, we also offer a wide range of value-added options, including a comprehensive project management service.
This includes:
- Advice and assistance on design for manufacture: we work with your engineers or scientists to help them perfect component or system designs, to ensure that they can be produced as efficiently as possible and to the highest levels of accuracy and quality.
- Advice on material selection: we’re used to working with many different metals, including exotic alloys and specialised hard materials, including Titanium Aluminide (TiAl), Aluminium Lithium (Al-Li) and Cobalt Chromium, and can provide guidance on the best metal for space and scientific applications.
- Project planning: ensuring that each project meets your specifications in terms of speed of response, deadlines, quality and delivery.
- Project delivery: engineering and finishing each component to your exact standards.
- Certification and traceability: full quality and process documentation produced to comply with the needs of your organisation.
Proactive communication: throughout, our engineering team keeps you up to speed with progress, advises you of any unexpected issues, offers solutions and provides ongoing advice and suggestions for future improvements.
Get in touch
Contact Frazer-Nash Manufacturing for a discussion of your specific requirements.
Call us on +44 (0)1730 230 340 or submit your enquiry using this form to request a call back.